La maintenance planifiée joue un rôle essentiel dans l’optimisation des systèmes de production. Dans un environnement commercial hautement compétitif et dynamique, les entreprises reconnaissent de plus en plus l’importance de maximiser la disponibilité et la fiabilité des équipements. Dans ce contexte, la maintenance planifiée apparaît comme une stratégie cruciale pour atteindre ces objectifs.
Face aux défis actuels, tels que l’augmentation de la concurrence, les pressions pour réduire les coûts et la recherche d’une plus grande efficacité, la maintenance planifiée devient un facteur distinctif. En investissant dans une approche systématique et proactive de la maintenance, les organisations peuvent maximiser la disponibilité et la fiabilité des équipements et des processus au moindre coût.
Introduction à la Maintenance Productive Totale (TPM)
Le TPM (Total Productive Maintenance) est une approche de gestion et de maintenance originaire du Japon, développée par le JIPM (Japan Institute of Plant Maintenance) dans les années 1970. Elle a été initialement introduite par Nippondenso, membre du Groupe Toyota, pour améliorer l’efficacité et la fiabilité des équipements.
Le TPM vise à atteindre l’efficacité maximale du système de production, impliquant tous les membres de l’entreprise dans l’élimination des pertes. Cette approche va au-delà de la maintenance conventionnelle, se concentrant sur l’excellence opérationnelle, la réduction des temps d’arrêt, l’amélioration de la qualité, l’augmentation de la productivité et la maximisation des ressources existantes. L’objectif est d’établir une culture de maintenance proactive et de responsabilité partagée.
Le TPM repose sur huit piliers, qui fournissent des directives pour une mise en œuvre réussie. La maintenance planifiée joue un rôle essentiel dans ce système, étant considérée comme l’un de ses piliers fondamentaux.
Qu’est-ce que la maintenance planifiée ?
La maintenance planifiée est une approche stratégique visant à maximiser la disponibilité et la fiabilité des équipements et des processus, tout en cherchant à minimiser les coûts. Elle repose sur des activités structurées et méthodiques, dans le but d’atteindre l’excellence dans la gestion des équipements.
La gestion du pilier de la maintenance planifiée doit être assurée par le responsable du département de maintenance, et la mise en œuvre des activités par l’équipe de maintenance.
Objectifs principaux de la maintenance planifiée
Assurer des équipements fiables et performants
Par des activités préventives et correctives, la maintenance planifiée vise à garantir que les équipements fonctionnent pleinement et sont dans des conditions optimales pour remplir leurs fonctions.
Optimiser le coût du cycle de vie des équipements
En planifiant et en exécutant des maintenances de manière organisée, il est possible de réduire les coûts en évitant les pannes et les ruptures inattendues, de prolonger la durée de vie des équipements et d’optimiser l’utilisation des pièces de rechange.
Former les personnes en contact avec l’équipement
La maintenance planifiée implique la formation et la qualification des opérateurs et des techniciens, afin qu’ils puissent jouer un rôle actif dans la maintenance et le soin des équipements, contribuant à l’efficacité et à l’efficience des opérations.
Contribuer à la création d’un environnement de travail sûr, agréable et motivant
Grâce à la maintenance planifiée, il est possible d’identifier et de corriger les risques potentiels pour la sécurité, offrant un environnement de travail plus sûr et stimulant.
Activités essentielles pour le fonctionnement de la maintenance planifiée
Au sein de la maintenance planifiée, plusieurs activités sont essentielles à son bon fonctionnement, parmi lesquelles nous soulignons :
- Activités de « panne zéro » : Elles comprennent l’enregistrement et l’analyse des pannes, ainsi que la révision des procédures de travail pour éviter les problèmes récurrents.
- Structuration et systématisation de la maintenance planifiée : Cela implique l’analyse du système existant, l’élaboration de diagrammes d’information et la définition de rapports standard pour la gestion de la maintenance planifiée.
- Gestion de la lubrification : Elle comprend la définition de types standard de contrôle visuel, des itinéraires standard de lubrification, ainsi que la planification générale de la lubrification des équipements.
- Gestion des pièces de rechange : Elle inclut la définition des emplacements de stock, la révision des spécifications et des quantités de pièces, et la révision du système de gestion des stocks pour assurer un approvisionnement adéquat.
- Gestion des coûts de maintenance : Elle implique la définition ou la révision des critères de classification, la mise en place d’un système de gestion des coûts et la définition des directives et des objectifs pour le contrôle et la réduction des coûts de maintenance.
- Gestion des maintenances programmées : Elle comprend la révision des systèmes de gestion des activités, la définition des types d’interventions et des critères pour la sélection de ces types d’interventions sur les équipements.
- Soutien à la maintenance autonome : Les équipes de maintenance ont également la responsabilité de soutenir la mise en œuvre des activités de Maintenance Autonome réalisées par les opérateurs des équipements.
Ces activités font partie intégrante de la maintenance planifiée et contribuent à la gestion efficace des équipements, garantissant leur disponibilité, fiabilité et performance optimisées.
Types d’actions de la maintenance planifiée
La maintenance planifiée implique la mise en œuvre de deux types principaux d’actions : Préventives et post-panne. Ces actions jouent un rôle fondamental dans la garantie de la disponibilité et de la fiabilité des équipements, minimisant le temps d’arrêt non planifié et améliorant l’efficacité opérationnelle.
Les actions préventives de la maintenance planifiée sont réalisées dans le but d’éviter les pannes des équipements. Parmi les principales actions préventives, on compte :
- Respecter les plans de maintenance, y compris l’exécution d’itinéraires standardisés : Les plans de maintenance contiennent les activités préventives planifiées pour chaque équipement, telles que les inspections, les lubrifications, les remplacements de pièces et les ajustements. En respectant ces plans, il est possible d’identifier et de corriger les problèmes avant qu’ils ne deviennent des pannes affectant le fonctionnement des équipements.
- Effectuer des restaurations et des remplacements pour rétablir les conditions d’origine : Grâce à la maintenance préventive, il est possible de restaurer les équipements pour retrouver leur état d’origine, en corrigeant l’usure et les dommages. De plus, si nécessaire, le remplacement de composants usés ou obsolètes contribue à maintenir l’efficacité et la performance adéquate des équipements.
- Améliorer les tâches pour éviter les pannes : Par l’analyse et la révision continue des tâches de maintenance, il est possible d’identifier des opportunités d’amélioration pour éviter les pannes. Cela peut impliquer l’optimisation des méthodes de travail, la mise en œuvre des bonnes pratiques et l’utilisation de technologies plus avancées.
- Former et mettre à jour les équipes sur les techniques de travail : La formation et la qualification appropriées des équipes de maintenance sont essentielles pour une exécution efficace des actions préventives.
- Quant aux actions post-panne de la maintenance planifiée, elles sont réalisées après une panne des équipements. Ces actions visent à enquêter et à corriger les causes racines de la panne afin d’éviter leur récurrence. Parmi les principales actions post-panne, on compte :
- Enquêter et enregistrer l’incident, en décrivant en détail les circonstances de la panne : Grâce à une enquête approfondie, il est possible de comprendre les circonstances dans lesquelles la panne s’est produite, en identifiant les facteurs qui ont pu contribuer au problème. En utilisant des méthodologies telles que les 5W1H.
- Effectuer une analyse de la panne pour découvrir la cause racine : L’analyse de la panne implique l’identification des causes racines qui ont conduit à l’incident. Cela peut être réalisé à l’aide de techniques telles que l’analyse de l’arbre des pannes, le diagramme d’Ishikawa (arête de poisson) ou d’autres méthodologies appropriées.
- Corriger la cause racine et proposer des mesures de blocage pour éviter les récidives : Sur la base de l’analyse de la panne, il est important de prendre des mesures correctives pour corriger les causes racines identifiées. Cela peut impliquer la mise en œuvre d’améliorations dans les processus, des ajustements sur les équipements, une formation supplémentaire ou d’autres mesures spécifiques. De plus, il est essentiel de proposer des mesures de blocage pour éviter la récurrence de la panne, telles que la mise à jour des standards, la modification des composants ou la mise en place de systèmes de surveillance.
En réalisant correctement les actions préventives et en mettant en œuvre les actions correctives nécessaires après une panne, il est possible de maximiser l’efficacité opérationnelle, de réduire les coûts et de minimiser l’impact des pannes sur les processus de production.
Bénéfices de la maintenance planifiée
La maintenance planifiée offre une série de bénéfices significatifs pour les organisations qui l’adoptent. Ci-dessous, nous décrivons certains des principaux avantages associés à la mise en œuvre efficace de la maintenance planifiée.
Augmentation du TRS (Taux de Rendement Synthétique)
Le TRS est un indicateur qui mesure l’efficacité globale d’un équipement ou d’un processus. La maintenance planifiée contribue à l’augmentation du TRS en améliorant la disponibilité des équipements. En planifiant et en exécutant des maintenances préventives de manière organisée, il est possible d’éviter les interruptions non planifiées, maximisant ainsi la disponibilité et l’utilisation des équipements.
Réduction des coûts de maintenance
La maintenance planifiée permet une approche proactive de la gestion des équipements, évitant les pannes inattendues et minimisant les réparations d’urgence coûteuses. En réalisant des maintenances préventives et correctives planifiées, il est possible de réduire les coûts associés à la maintenance non planifiée, tels que les arrêts de production, l’achat de pièces de rechange d’urgence et la sous-traitance de services urgents.
Concentration des techniciens de maintenance sur des tâches avancées
Avec la maintenance planifiée, les techniciens de maintenance peuvent se concentrer sur des tâches plus avancées, telles que l’analyse de données, le diagnostic de problèmes complexes, l’implémentation d’améliorations sur les équipements et l’optimisation des processus. En réduisant le besoin d’interventions d’urgence, les techniciens disposent de plus de temps et de ressources pour se consacrer à des activités à plus forte valeur ajoutée.
Augmentation de la durée de vie utile des équipements
La maintenance planifiée joue un rôle crucial dans la préservation et l’extension de la durée de vie des équipements. En réalisant des maintenances préventives, des inspections régulières et une lubrification adéquate, il est possible d’identifier et de corriger les problèmes avant qu’ils ne s’aggravent et ne causent des pannes majeures sur les équipements. Cela se traduit par une plus grande durabilité des équipements, réduisant le besoin de remplacements prématurés et augmentant le retour sur investissement.
Amélioration de la sécurité des équipements
La maintenance planifiée contribue à améliorer la sécurité des équipements et la fiabilité des opérations. En identifiant et en corrigeant les problèmes potentiels avant qu’ils ne causent des pannes, la maintenance planifiée aide à prévenir les accidents, à minimiser les risques et à créer un environnement de travail plus sûr.
Amélioration de la qualité du produit
La maintenance planifiée joue également un rôle dans le contrôle de la qualité du produit. En évitant les pannes et les problèmes sur les équipements, la maintenance planifiée réduit l’occurrence de défauts de qualité et les retouches.
En mettant en œuvre efficacement des stratégies de maintenance planifiée, les organisations peuvent obtenir un avantage compétitif significatif sur le marché.
Étapes pour la mise en œuvre de la maintenance planifiée
La mise en œuvre de la maintenance planifiée se déroule en 6 étapes que nous décrivons ci-après.
Évaluation de la situation actuelle et organisation des données techniques
À cette étape initiale, il est essentiel d’évaluer la situation actuelle des équipements et d’organiser les données techniques pertinentes. Cela implique de développer ou de mettre à jour les registres des équipements, d’établir des critères d’évaluation et de définir des priorités pour les équipements et les composants pour la maintenance productive. De plus, il est nécessaire de comprendre la situation actuelle en mesurant le nombre, la fréquence et la gravité des pannes, les petites interruptions, le MTBF (Mean Time Between Failures), les coûts de maintenance, les taux de panne de maintenance, entre autres. Établir des objectifs clairs pour la maintenance, en définissant des indicateurs et des méthodes pour mesurer les résultats, est également fondamental à cette étape.
Système pour la gestion des activités de support
À cette deuxième étape, il est nécessaire d’établir les conditions de base pour inverser la détérioration et éliminer les environnements qui causent une détérioration accélérée. Cela peut impliquer la mise en œuvre d’activités d’amélioration spécifiques pour corriger les points faibles et prolonger la durée de vie des équipements. De plus, il est important de prendre des mesures pour empêcher la répétition de pannes identiques ou similaires et d’introduire des améliorations pour réduire les défaillances du processus.
Structuration du système de gestion de l’information
La troisième étape concerne la structuration d’un système de gestion de l’information. Cela comprend la création d’un système de gestion des données de panne, d’un système de gestion de la maintenance des équipements pour le contrôle des historiques, la planification de la maintenance, les inspections, entre autres. Il est également nécessaire d’établir un système de budgétisation de la maintenance / équipements et un système pour contrôler les pièces de rechange, les dessins, les spécifications, entre autres.
Structuration du système de maintenance périodique
À cette étape, il est important de préparer la maintenance périodique, incluant le contrôle des pièces de rechange, des instruments de mesure, des lubrifiants, des dessins et des données techniques. Il faut préparer un diagramme de flux du système de maintenance périodique, sélectionner les équipements et les composants qui seront soumis à la maintenance périodique et élaborer un plan de maintenance. De plus, il est nécessaire de développer ou de mettre à jour des procédures, telles que les procédures de matériaux, opérationnelles, d’inspection, d’approbation, entre autres. L’efficacité de la maintenance en cas de panne doit également être améliorée, ainsi que le contrôle des services externes.
Structuration du système de maintenance prédictive
À la cinquième étape, il est essentiel d’introduire des techniques de diagnostic d’équipements. Cela inclut la formation des évaluateurs et l’acquisition d’instruments de diagnostic. Il faut préparer un diagramme de flux du système de maintenance prédictive, sélectionner les équipements et les composants qui seront soumis à la maintenance prédictive et, progressivement, étendre cette pratique. De plus, il est important de développer des équipements et des instruments de diagnostic, ainsi que la technologie associée à ceux-ci.
Évaluation du système de maintenance planifiée
La dernière étape est l’évaluation du système de maintenance planifiée. À cette étape, il est nécessaire d’évaluer l’amélioration de la fiabilité des équipements, en tenant compte du nombre de pannes et de petites interruptions, du MTBF, de la fréquence des pannes, parmi d’autres indicateurs. Il est également important d’évaluer l’amélioration de la maintenabilité, en considérant le taux de maintenance périodique, le taux de maintenance prédictive, le MTTR (Mean Time To Repair), parmi d’autres indicateurs. Enfin, il est nécessaire d’évaluer la réduction des coûts, y compris la réduction des dépenses de maintenance et l’amélioration de la répartition des ressources de maintenance.
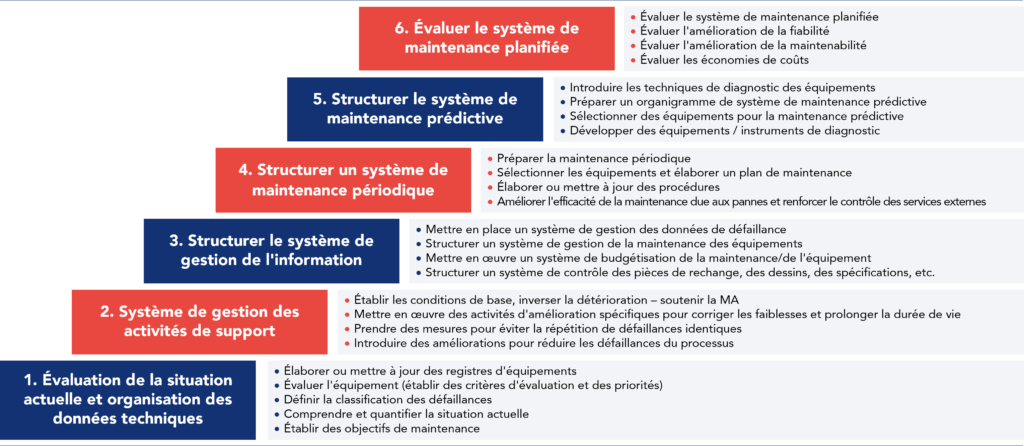
En suivant ces 6 étapes, il est possible de mettre en œuvre efficacement la maintenance planifiée, maximisant la disponibilité et la fiabilité des équipements, optimisant les coûts et garantissant un environnement de travail sûr et productif.
Relation de la maintenance planifiée avec les autres piliers du TPM
La maintenance planifiée joue un rôle fondamental au sein du TPM. La relation de la maintenance planifiée avec les autres piliers du TPM est de complémentarité et de soutien mutuel.
Par exemple, la maintenance planifiée est étroitement liée au pilier de la maintenance autonome, où les opérateurs jouent un rôle actif dans la maintenance des équipements. Grâce à la maintenance planifiée, les opérateurs reçoivent le soutien adéquat et des orientations sur les actions de maintenance à réaliser.
De plus, la maintenance planifiée est liée au pilier de l’amélioration spécifique. Grâce à l’analyse des données et des informations sur les pannes, la maintenance planifiée permet d’identifier les pannes récurrentes et de mettre en œuvre des actions correctives pour éliminer les causes racines. Tout cela est conforme à l’objectif de l’amélioration spécifique qui consiste à accroître la fiabilité et les performances des équipements.
Ce ne sont que des exemples de l’interaction et de la complémentarité entre les piliers. Dans le tableau suivant, il est possible d’observer les activités qui se déroulent en parallèle et se complètent.
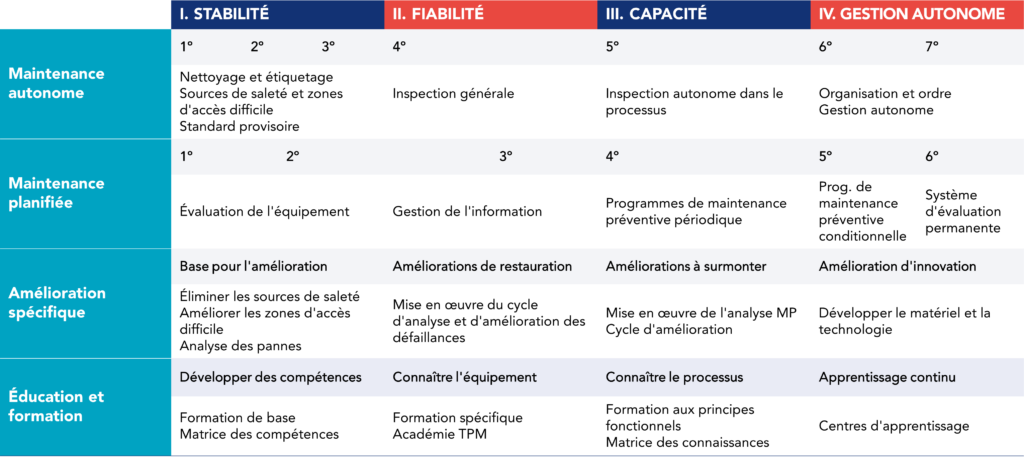
En résumé, la maintenance planifiée est un élément essentiel du TPM, qui travaille en conjonction avec les autres piliers pour atteindre l’efficacité, la fiabilité et la productivité maximales des équipements et des processus de production.
Avez-vous encore des questions sur la maintenance planifiée dans le cadre de la gestion des équipements ?
Qu’est-ce que la disponibilité d’un équipement ou d’un système ?
La disponibilité est la probabilité qu’un équipement / système soit dans des conditions idéales à un moment donné.
Qu’est-ce que la fiabilité d’un équipement ou d’un système ?
La fiabilité est la capacité d’un équipement / système à remplir une fonction requise dans des conditions prédéfinies et pendant une période de temps déterminée.
Qu’est-ce que les 5W1H ?
La méthodologie des 5W et 1H est une technique d’analyse de problèmes qui consiste à poser une série de questions clés pour obtenir des informations complètes et pertinentes sur un sujet donné.
Les 5W et 1H représentent les questions en anglais :
- What? (Quoi ?) : Se réfère au problème ou au sujet en cours d’analyse. Qu’est-ce qui s’est passé ? Quel est l’objectif ? Quel est le contexte ?
- Who? (Qui ?) : Identifie les personnes ou entités impliquées dans le problème. Qui sont les personnes affectées ? Qui sont les responsables de la résolution du problème ?
- When? (Quand ?) : Se réfère au temps ou au moment du problème. Quand cela s’est-il produit ? Quand doit-il être résolu ? Quelle est la date limite ?
- Where? (Où ?) : Indique le lieu ou le contexte spatial du problème. Où cela s’est-il produit ? Où est-ce situé ? Où doit-il être résolu ?
- Why? (Pourquoi ?) : Cherche à comprendre les raisons ou les causes du problème. Pourquoi cela s’est-il produit ? Pourquoi est-il important de résoudre ce problème ? Quelles sont les conséquences ?
- How? (Comment ?) : Explore les solutions ou méthodes possibles pour résoudre le problème. Comment pouvons-nous aborder le problème efficacement ?
En répondant à ces questions, la méthodologie des 5W et 1H aide à obtenir une compréhension complète du problème, à identifier les informations nécessaires et à élaborer un plan d’action plus efficace pour le résoudre.
Qu’est-ce que la maintenance corrective ?
La maintenance corrective est une stratégie de maintenance qui consiste à effectuer des réparations et des interventions sur des équipements, des machines ou des systèmes uniquement lorsqu’une panne ou une défaillance se produit. La maintenance corrective n’intervient qu’après l’apparition d’un problème.
Qu’est-ce que la maintenance préventive ?
La maintenance préventive est une stratégie de maintenance qui consiste à effectuer des actions planifiées et systématiques pour éviter les pannes, réduire l’usure et prolonger la durée de vie des équipements, des machines ou des systèmes. Au lieu d’attendre qu’une panne se produise et de prendre des mesures correctives, la maintenance préventive implique des inspections, des tests, des nettoyages, des lubrifications et des remplacements de pièces réguliers, selon un calendrier prédéterminé.
Qu’est-ce que la maintenance par amélioration ?
La maintenance par amélioration comprend des activités qui préviennent les pannes futures des équipements, facilitent l’inspection, la réparation et l’utilisation, et garantissent la sécurité.
Qu’est-ce que la prévention de la maintenance ?
La prévention de la maintenance signifie que lors de la conception ou de l’acquisition d’un équipement, il faut prendre en compte si ces derniers nécessiteront peu ou pas du tout de maintenance.
Qu’est-ce que la maintenance productive ?
La maintenance productive est celle qui prend en compte et optimise l’utilisation des quatre types de maintenance : maintenance corrective, maintenance préventive, maintenance par amélioration et prévention de la maintenance.
Maintenance
Découvrez comment améliorer ce secteur d’activité